The international standard ISO 26262 Functional Safety of Road Vehicles is a functional safety standard for eight seat passenger vehicles with a gross weight of not more than 3.5 tons and based on the characteristics of safety related electrical and electronic systems. It was developed based on IEC 61508 Functional Safety of Safety Related Electrical/Electronic/Programmable Electronic Systems and officially released on November 15, 2011, This standard poses a new challenge to automobile manufacturers: it is necessary to test the controllability of the vehicle when the sensor fails. ISO26262 has been formally formulated since November 2005. After about six years, it was officially issued in November 2011 and became an international standard. The national standard GB/T34590 was released in 2017, which is basically consistent with ISO26262.
Safety is one of the key elements in the future automobile research and development. The new functions are not only used to assist driving, but also used in the dynamic control of vehicles and active safety systems related to safety engineering. In the future, the development and integration of these functions will certainly strengthen the requirements of the security system development process, and also provide evidence to meet all expected security purposes. With the increase of system complexity and the application of software and electromechanical equipment, the risk of system failure and random hardware failure is also increasing. The purpose of formulating ISO 26262 standard is to make people have a better understanding of safety related functions, explain them as clearly as possible, and provide feasible requirements and processes to avoid these risks.
In practice, this means that the test department needs to collect vehicle performance data under various driving operations when a sensor fails. The difficulty of this test is that the acquisition of high-precision position (± 3cm) data, ECU internal data, sensor signals, vehicle CAN bus data and other signals, even including video signal acquisition, must be synchronized. The following is a specific example.
Specific cases
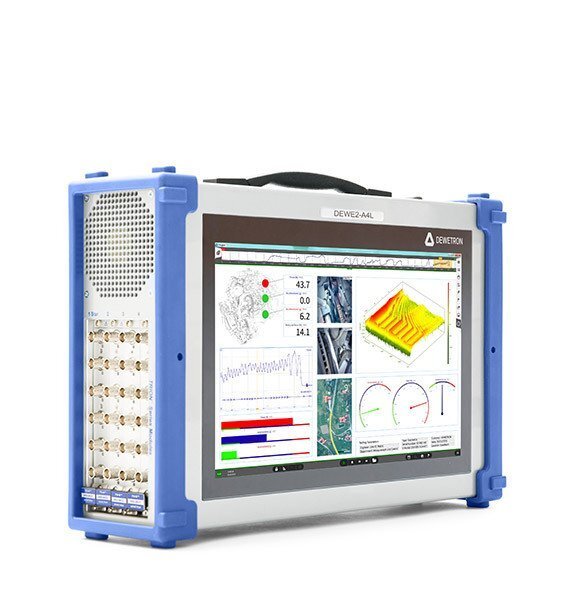
A customer asked Devtrong to help him test the yaw of the vehicle when a heading angular speed sensor failed. This kind of test has also been done before, but at that time, the driver's subjective feeling was only used to judge the dangerous degree of driving operation, which did not conform to the new ISO standard. In order to obtain objective data, the customer is equipped with a set of test instruments of DVC, including a gyroscope/GPS system and a DGPS base station installed in the test site. The position measurement accuracy of the system reaches ± 3 cm.
The customer's actual test situation is: the driver drives the vehicle on a circular loop at an angular speed of about 20 °/s, and simulates the failure of the heading angular speed sensor by adding a step function signal to the CAN bus signal; The test result shows that the car deviates from the original track by 3.5m.
Once the yaw rate sensor fails, the vehicle may deviate to another lane and cause traffic accidents. Of course, the customer's goal is to control the vehicle normally at any time. Therefore, the ESP system installed on the vehicle needs to be improved. The customer not only wants to get the result of the vehicle deviation from the track, but also needs to understand the data inside the ECU. The internal data of most ECUs can be read through a special interface (network port XCP protocol). Dewei Chuang supports the network port XCP protocol, so the ECU is like an intelligent sensor for the Dewei Chuang system.
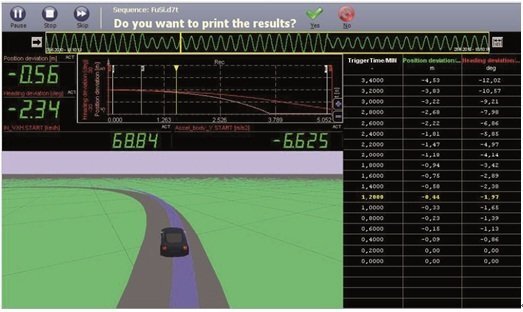
Test completion screen
In order to improve the ESP system, we need to synchronously collect ECU internal parameters during the test. Compared with the test data, we found that the ESP system did not fully check the authenticity of the heading speed sensor signal. In this case, the ESP should determine that the sensor signal is wrong.
The ECU software control algorithm can be improved and verified by using the Devtrong test system, so as to judge whether the sensor signal is true or false, so as to control the vehicle correctly.
After the ESP is improved, the same test is carried out again. The ESP can judge that the heading angular velocity sensor signal is invalid, so there will be no action. In this way, the vehicle will not change the driving track to ensure safety.
testing procedure
In order to test the controllability of the vehicle when the heading angular speed sensor fails, two tests are required: driving at a constant speed in a straight line, or driving on a circular road with a constant lateral acceleration of 0.5g; Drive on a specific curve (such as the route specified in the ISO lane change test). If the ECU has a fault signal, the car may slip and deviate from the lane. Devtrong system has prepared system configuration files for two tests. These system configuration files can be used for various other test projects with slight modification.