Application of DVC Data Acquisition in Dynamic Temperature and Pressure Measurement of Aircraft Turbine Engine
Application background
This research involves the dynamic temperature and pressure measurement data obtained inside the aircraft propulsion turbine engine. An important factor causing aircraft noise is the internal noise generated by the propulsion engine. This topic has become increasingly important in the past few years. In particular, combustion noise, as an important noise source, has attracted attention. There are two main sources: direct and indirect combustion noise, both of which come from sound waves propagating through the engine core. Sound waves are generated by random pressure fluctuations. The pressure fluctuation caused by unsteady heat release in turbulent combustion process leads to direct combustion noise.
Pressure fluctuation, which is indirectly generated entropy fluctuation, is also generated by turbulent combustion process, resulting in indirect combustion noise. These entropy fluctuations convection through the mean velocity gradient. The coupling between this entropy and the pressure disturbance produces these pressure fluctuations. For different directions, there are also different challenges. From an empirical point of view, it is challenging to obtain data in the harsh internal space of the engine combustion chamber. From the perspective of data analysis, it is challenging to distinguish between direct noise and indirect noise. Finally, from the perspective of simulation, it is challenging to simulate the complex random acoustic processes that occur in the engine core. This paper mainly studies the measurement of dynamic temperature and pressure, which simultaneously obtain the engine core of the propulsion engine, as shown in the figure. The engine is equipped with a two-stage high-pressure turbine (HPT) and a three-stage low-pressure turbine (LPT).
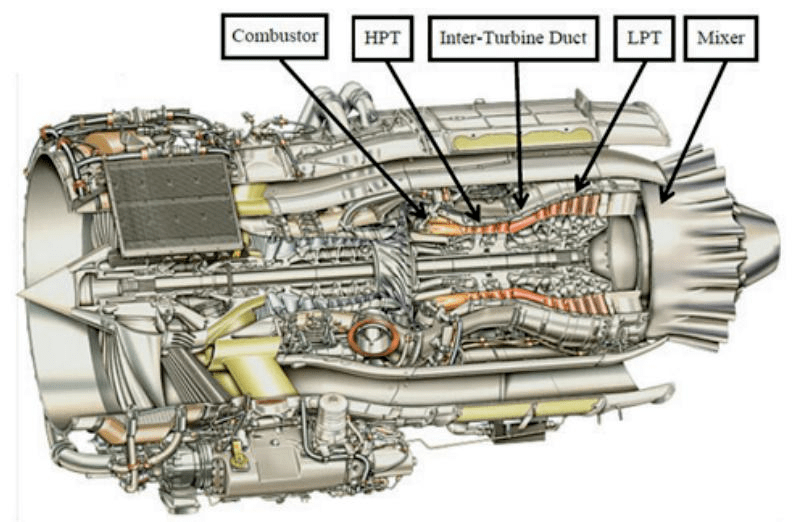
Temperature Measurement of Aircraft Turbine Engine
For temperature measurement, dual thermocouple probe and piezoresistive sensor for pressure measurement are used. In order to obtain the voltage signal of the probe, we used a desuperheating probe system. For data DEWETRON The data collection system of 10-20 kHz To address temperature fluctuations up to 1000 Hz in the burner to cover the fre related condition range. Different measurements were made under four steady-state operating conditions, in which combustion noise contributed to aircraft noise levels. The measurement results were carried out at 48%, 54%, 60% and 65% of the corrected fan speed (NFC), respectively. The recording length of data acquisition at each speed is 70 seconds. The following figure shows a clip of five temperature probes measuring at 48% speed, located on the left side of the engine. The data of small wires and large wires are shown in blue and red, and the average value is subtracted to better show the fluctuation. As expected, the fluctuations of the two conductors vary roughly in unison. However, the change of small wires is faster, because the thermal mass of small wires is smaller, and the temperature fluctuation and cooling speed reach greater extreme values faster. The peak temperature fluctuation amplitude of the burner is one order of magnitude larger than that of the turbine pipe upstream of the LPT, which is about twice the peak temperature fluctuation of the mixer downstream of the LPT.
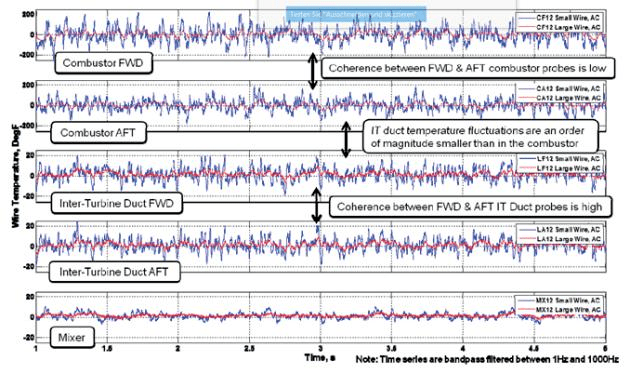
Application summary
Through the measurement, a database of dynamic temperature and pressure data can be obtained in the internal core of the propulsion engine. They found that the temperature fluctuation upstream of HPT was one order of magnitude larger than that measured upstream of LPT. In addition, the temperature fluctuation is quite constant and does not change too much with the engine speed. These results will be helpful to further study the generation of combustion noise in practical applications.
Product recommendation:
Dewei Chuang Data acquisition integrated machine DEWE3-A4
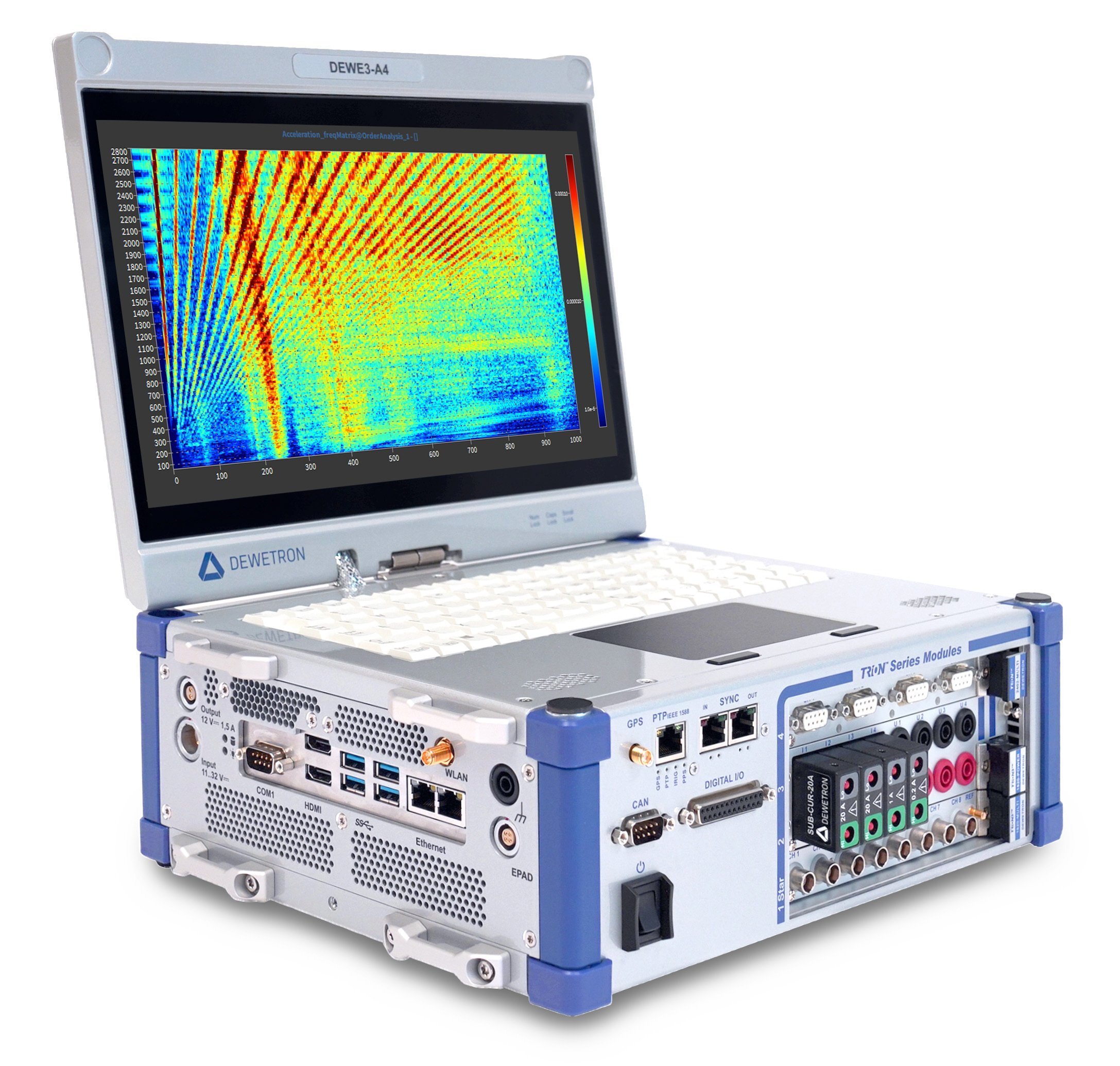
All in one measurement system with built-in display
TRION loadable ™/ TRION 3 ™ modular
Extremely high channel density
User replaceable TRION/TRION 3 module for analog quantity, digital quantity, counter and CAN bus input
Selectable resolution up to 24 bits