The Application of Dewei Chuang Large Data Acquisition in the Hydraulic Landing Device Test System
Hydraulic Landing Device Test System of a Design and Research Institute of AVIC
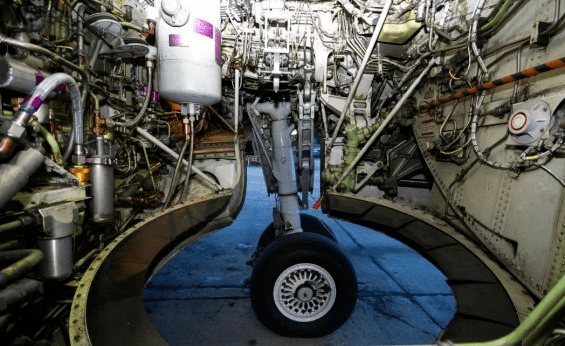
Project Background: One of the comprehensive test facilities for hydraulic and landing gear systems of an aircraft.
It is mainly used for hydraulic energy system test and landing gear system test to complete the collection and recording of dynamic and static parameters such as pressure, flow, displacement, temperature, vibration, stress, etc. in hydraulic pressure and landing gear system test, data analysis and processing, as well as the analysis and calculation of various test state performance parameters, and can display test curves in real time, save and manage test data in real time.
Composition of data test system:
Landing gear test data acquisition system
Hydraulic test data acquisition system
Conduit stress and strain measurement system
Vibration measurement system.
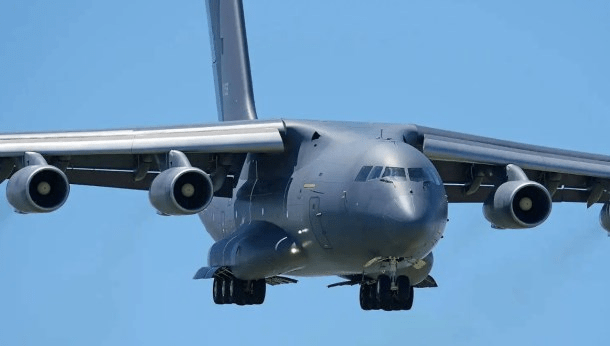
Composition of data acquisition equipment: ( three hundred and thirty-two simulation +36 Counter +40 Temperature)
DEWE2-M18 * 5 Set
TRION-1603-LV-6-BNC * 30 Zhang
TRION-2402-dACC-6-BNC * 12 Zhang
TRION-2402-dSTG-8 * 10 Zhang
TRION-BASE * 3 Zhang
TRION-CNT-6-L1B * 5 Zhang
EPAD2-RTD8-L1B *5 Pieces
Test signal:
stress / Strain pressure pulsation flow / Velocity vibration temperature
Project characteristics:
➢ The signal type is complex, dynamic and static signals are collected at the same time, and the module is required to set the sampling frequency separately;
➢ The real-time remote transmission function of test data is required to realize data sharing while data acquisition, storage and analysis;
➢ It has the sensor calibration function to calibrate the primary coefficient and constant of the sensor;
➢ Each part can run independently, or network synchronization test can be conducted; Capacity improvement:
➢ dynamic / The static signal test system is integrated, and all signal time axes are synchronized;
➢ Networked synchronous acquisition and remote software control;
➢ The test data is transmitted to the remote computer (outside the system) in real time for special software calling for processing and analysis;
➢ Realization of large-scale comprehensive test capability