What is order analysis?
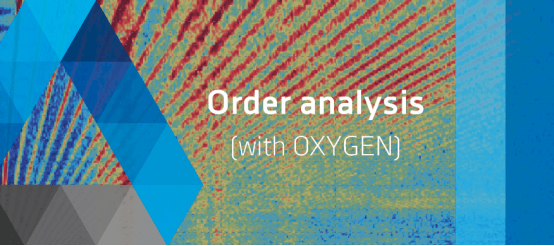
In rotor dynamics, order analysis (or order tracking) is the analysis of noise or vibration of rotating machinery or vibrating parts. It is based on vibration and velocity measurement, which requires at least one acceleration sensor to evaluate the vibration of the DUT. In addition, it is necessary to determine or estimate the speed and angular position of the rotor. This is usually done with an encoder or tachometer.
In the world of rotating machinery, vibration tells a silent but powerful story - especially when studying through order analysis. Based on vibration and rotation measurement, it provides engineers with various insights into the inspected system. Let's have a deep understanding of the basic principle of order analysis and discover its core role in maintaining the health and reliability of machinery.
In contrast to frequency analysis, the energy content of noise or vibration is not plotted by frequency, but by order. In this case, order refers to the harmonic component of the vibration signal. Each step corresponds to a multiple of the basic speed of the rotor. In other words, this means that the first order corresponds to the speed of the rotor itself, the second order corresponds to twice the speed, and so on. Each order represents a harmonic component in the vibration signal.
How to do order analysis?
First, we need to collect vibration data from the DUT (e.g. engine), such as using an accelerometer. Generally speaking, in the next step, we remove any irrelevant data (noise) from the original vibration signal and only capture the relevant frequency range. We also need a signal that provides information about the rotor speed of the equipment being tested. This can be collected using, for example, a tachometer.
Before we start the order analysis, we need to ensure that our vibration data is synchronized with the rotation (or angular position respectively) of the rotor. For example, this can be achieved by simultaneously recording speed pulses.
Once we have determined a single rotation (corresponding to the first order), we apply the tracking algorithm to track the frequency change of each order over time. Therefore, we divide the vibration signal into signal blocks of one revolution, one of which represents one revolution.
In order to improve the results and avoid inaccurate results, we applied further filtering (such as anti aliasing filter), smoothing and resampling operations., We use fast Fourier transform (FFT) to transform each block into frequency domain. This gives the power spectrum of each angular velocity [rpm].
The results can then be visualized in various graphs. However, in order tracking, we usually use the 2d color image representing the vibration intensity as the color of spectrum and RPM. This spectrum can be visualized as spectrum or order spectrum. The order spectrum relates the frequency component of the acceleration signal to the order of the mechanical speed. This allows intuitive tracking of orders at different speeds in the order spectrum representation, and tracking of frequency components in the spectrum representation.