Introduction to air explosion test
Air explosion test is not only for aerospace and defense departments An important test component In other occasions, explosion is also an important part of the test procedure, such as airbag, and explosion test is also used for testing Vehicle protection Structural integrity. The analysis of the air explosion shock wave test is of great significance for characterizing the rapid release of the energy generating the pressure wave and restoring it to normal environmental conditions. Therefore, different types of tests can be carried out, such as free air, directional or contained air explosion, to measure the generated shock wave. This process is a highly dynamic event. Therefore, a highly dynamic DVI measurement system is required to capture all data for important evaluation. Incomplete or lost data will have unacceptable impact on the product and must be avoided in any possible way. A high reliable measurement system with high sampling rate is required to meet all these requirements.
Air explosion test challenge and DVC solution
In order to avoid measurement errors, there are many things to pay attention to, such as selecting the correct one in this harsh environment sensor At the same time, selecting the correct measurement system will also help the measurement process. Knowing that you can perform reliable measurements without losing any data can prevent frustration because there is only one chance to perform an explosion test. For explosion tests, different types of sensors are used. Accelerometers (such as PCB 3503A1160KG, DTS 6DX PRO, Endevco 7270A), force and strain sensors are usually required to measure DUT (such as PCB 740B02), pressure sensors (such as PCB 137B24B) or temperature sensors (such as Exergen IRt/c.100A) to measure wave propagation. To achieve successful results, all of these sensors can communicate with TRION3 -1850-MULTI. The high sampling rate of 5 MS/s for each channel ensures the capture of all important data generated by air explosion. The event that the pressure wave reaches the peak only lasts for a few microseconds, rather than a linear process. Therefore, it is important to have as much information as possible to reconstruct this event. Therefore, high sampling rate, excellent AC accuracy and high dynamic range (140 dB signal-to-noise ratio) are necessary. The influence of different sampling rates is shown in the figure. In addition to the high sampling rate of each channel, all data of each channel has different types of sensors (such as IEPE ®、 Voltage, bridging, etc.). The same measuring amplifier is used for measurement, so as to ensure perfect synchronization of channel to channel phase mismatch less than 10ns. This is one of the key features of TRION3-1850-MULTI, which is very beneficial to successful measurement and results.
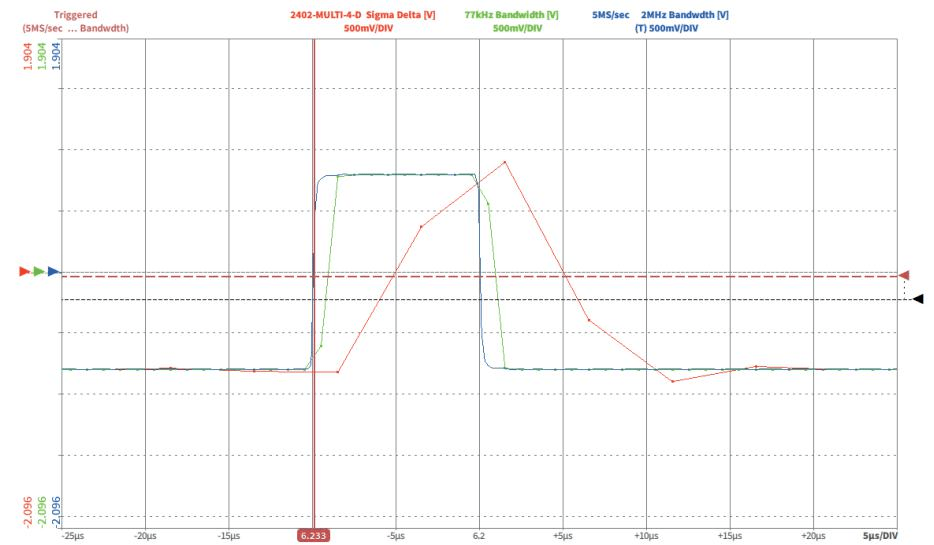
Influence of different sample rates on step response
In order to measure the expansion of the shock wave, the sensors can be distributed in multiple locations. Therefore, long cables must be used in this harsh environment. When using IEPE ® (Integrated electronic piezoelectric) sensors require high current to drive the signal from the source to the measurement system without limiting the rotation rate. In order to do this, a large current is required, otherwise the signal will be attenuated and distorted by the measurement results. For a test that can only be executed once, this is a very undesirable impact. Generally, IEPE ® The internal electronic equipment of the sensor is powered by a 4 mA or 8 mA constant current source of the data acquisition system. Considering that the sensor itself needs about 1 mA, there is not much left to drive the signal through the line. As shown in the following formula, there is an inverse relationship between voltage and capacitance, because C is the cable capacitance.
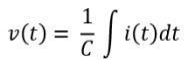
To calculate the maximum undistorted frequency for a specific signal amplitude, the following equation represents an approximation.
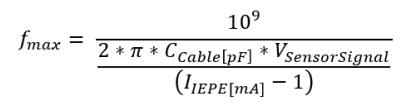
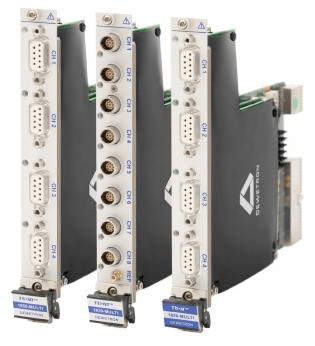
The multi-channel data acquisition module TRION3-1850-MULTI of DVC has a bandwidth of 2 MHz and a bandwidth of up to 20 mA Free programmable IEPE for ® Excitation current to avoid any harmful effects of voltage signal attenuation. Strain gauges and bridge circuits are also used to record explosion test data. For this high-speed measurement, it is recommended to use a full bridge circuit. The reason is the resulting differential output signal. The advantage of differential signal is that external interference is common mode interference, so it can be damped by common mode suppression. TRION3-1850-MULTI supports not only different bridge types, such as quarter bridge, half bridge and full bridge, but also different line connections, depending on the connection circuit of the bridge. For example, the module supports the connection between the 2-wire, 3-wire and 4-wire quarter bridge and the internal bridge to complete 120 Ω, 350 Ω and 1000 Ω. Another advantage of TRION3-1850-MULTI is its easy to use filter settings. By default, the input signal is low-pass filtered with the 8th order Bessel filter, and the cut-off frequency is 30% of the sample rate. With these settings, it will ensure that no aliasing effect occurs, and the signal will not be distorted. While Butterworth filter may have higher AC accuracy, it shows an oscillation - for step response. Bessel filter is more convenient than Butterworth fast and transient event filter, because it has better step response. An example of step response is with these two types of filters, Bessel and Butterworth. In addition, TRION3-1850-MULTI uses SAR ADC instead of Sigma Delta( ΣΔ) ADC。 This is a great benefit when measuring fast events. And ΣΔ Compared with ADC, the delay between input and output of SAR ADC is much smaller. In addition, SAR ADC has a very low noise floor, which results in a very high dynamic range and signal to noise ratio of 140 dB, as mentioned earlier. All these advantages make SAR ADC a better choice for measuring fast and transient events.
Air explosion test conclusion
The explosion test should not only be carried out under bad conditions, but also not be repeated effortlessly. Especially for this reason, it is necessary not only to have a good sensor selection, but also to have a reliable measurement system. In order to maximize the use of a few seconds of an explosive test, the high-end TRION3-1850-MULTI is a perfect solution to capture all data at a high sampling rate of 5 MS/s per channel. 2 MHz bandwidth, freely programmable IEPE ® The excitation current is up to 20 mA, and the simple filter is set to synchronize perfectly with all channels of different sensor types, ensuring good measurement results.