In the world of automotive engineering and embedded systems, precision and control are extremely important. Whether it is to fine tune engine performance, optimize fuel efficiency, or ensure the safety of advanced driving aids, the ability to accurately measure and calibrate components is essential. This is where XCP comes into play. XCP plays a key role in helping engineers and developers improve the performance and functionality of equipment and systems. In this blog post, we will go deep into the world of XCP and explore its origin, application and importance.
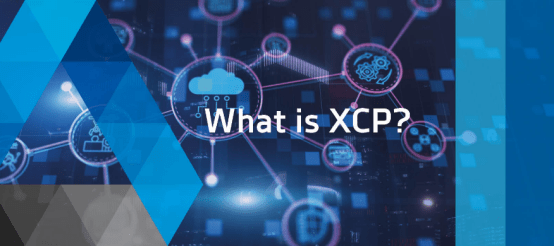
What is XCP?
XCP is a standardized network protocol, representing a universal measurement and calibration protocol. The first letter X indicates that the protocol is designed for various bus systems. The protocol provides a standardized communication interface between the calibration tool (usually PC) and the embedded electronic control unit (ECU). XCP simplifies the process of accessing and adjusting parameters, enabling engineers to fine tune and optimize the performance of ecu.
XCP was established by ASAM (Association for Standardization of Automation and Measurement Systems) in 2003 to solve the increasingly complex problem of automotive embedded systems. As vehicles become more advanced and complex, engineers need a more effective way to calibrate and fine tune these systems. The previously popular CAN calibration protocol (CCP) could not meet these challenges, and XCP was introduced as a successful solution.
What are the benefits?
Compared with its predecessor CCP, XCP provides several advantages. The main features are:
efficiency
XCP is specially designed for high-speed data exchange, which can quickly read and write data to ECU. This is critical when real-time adjustment of ECU parameters is required. In addition, it measures ECU time stamp and higher Data throughput Provides more accurate data collection.
flexibility
XCP is a two-layer protocol, which means that it always separates the protocol layer from the transport layer. This makes it particularly versatile because it can handle various transport layers by always using the same protocol layer. XCP supports synchronous and asynchronous serial interfaces, such as CAN (FD), Ethernet, FlexRay, SxL, etc. This makes XCP very versatile and suitable for various tasks such as flashing new firmware, monitoring sensor data, and calibrating control parameters.
XCP protocol and transport layer
security
XCP protocol usually has built-in security features, such as encryption and authentication, to protect sensitive data and prevent unauthorized access. This is particularly important in today's increasingly concerned automotive industry.
Although XCP provides many advantages, CCP is still used. Especially when the compatibility of legacy systems and existing infrastructure is a problem, CCPs have reasons to use them. However, with the continuous development of the automotive industry, XCP's advantages in speed, efficiency and versatility make it the main choice for many modern vehicle calibration and measurement tasks.
Where is XCP applied?
As we have established many times, XCP is mainly used in the automotive industry. It is a basic tool to calibrate and optimize the performance of vehicle ecu. In addition, it plays a vital role in the calibration of electric and hybrid vehicle systems. It can precisely control battery management, motor behavior and energy consumption.
However, the automotive industry is not the only application area. Its flexibility and general applicability make it a valuable tool for developers in other fields. In the aerospace industry, XCP is used to calibrate and fine tune avionics systems and sensors. In addition, in the field of industrial automation, it assists the automation system to ensure accurate and reliable operation.
XCP function of Dewei Chuang OXYGEN software
If you don't know: OXYGEN software is our intuitive data acquisition software. It is a multi-functional but easy to use measurement software for various fields. In addition to measuring and recording data, OXYGEN can also:
Data analysis and post-processing
Power and efficiency analysis
Sound level analysis
Sequence analysis
System monitoring
And more
Because it can be used for many different applications, OXYGEN also supports a variety of network protocols and transmission interfaces, including CAN, FlexRay, EtherCAT, XCP, etc. Therefore, if your test bench needs XCP, just select our optional XCP software option. This allows OXYGEN software to act as a slave to XCP and provide measurement data to your system.